BENEFITS OF USING NEOPOR® CCYCLED® EPS
- Ensures the same mechanical characteristics as conventional Neopor®, such as all-around high impact energy absorption
- Saves fossil resources and reduces CO2 emissions compared to conventional EPS
- Contributes to a circular economy by turning plastic waste into feedstock for the chemical industry, when no other recycling processes are applicable
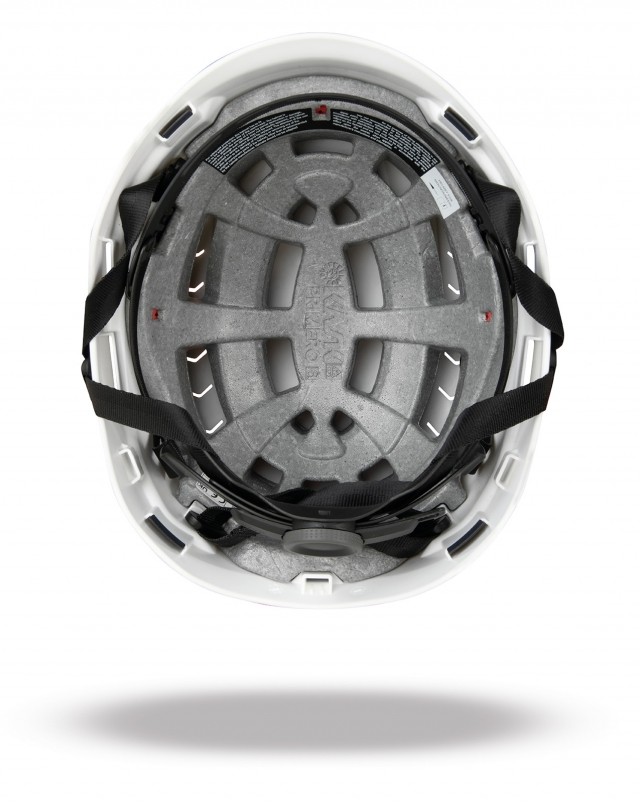
REDUCED PRODUCT CARBON FOOTPRINT
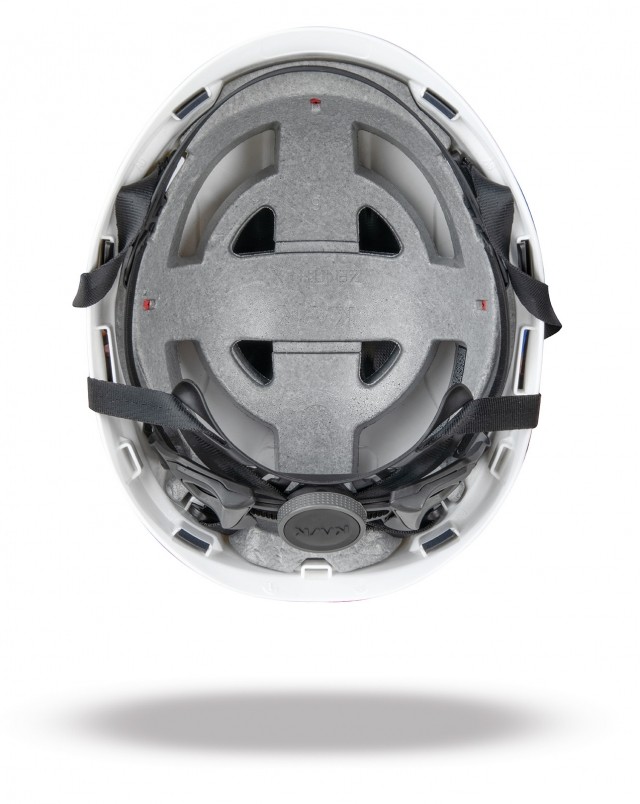
Neopor® Ccycled® has a product carbon footprint reduced by about 90% compared to conventional Neopor® produced on the basis of fossil feedstock.
CO2 emissions are saved when manufacturing EPS using pyrolysis oil under a mass balance approach*. The lower emissions result from chemically recycling the mixed plastic waste instead of incinerating it.
THE PRODUCTION PROCESS
CONSERVING RESOURCES
Consumers dispose plastic products
Plastic waste is sorted and delivered to BASF technology partners
Plastic waste is chemically recycled and converted into pyrolysis oil
The pyrolysis oil obtained is used as feedstock at the very beginning of the BASF value chain
The pyrolysis oil is attributed to Neopor® Ccycled® via a certified mass balance approach*
New products, e.g. internal shell of KASK safety helmet, are manufactured from Neopor® Ccycled®
Consumers dispose plastic products
New products, e.g. internal shell of KASK safety helmet, are manufactured from Neopor® Ccycled®
The pyrolysis oil is attributed to Neopor® Ccycled® via a certified mass balance approach*
Plastic waste is sorted and delivered to BASF technology partners
Plastic waste is chemically recycled and converted into pyrolysis oil
The pyrolysis oil obtained is used as feedstock at the very beginning of the BASF value chain